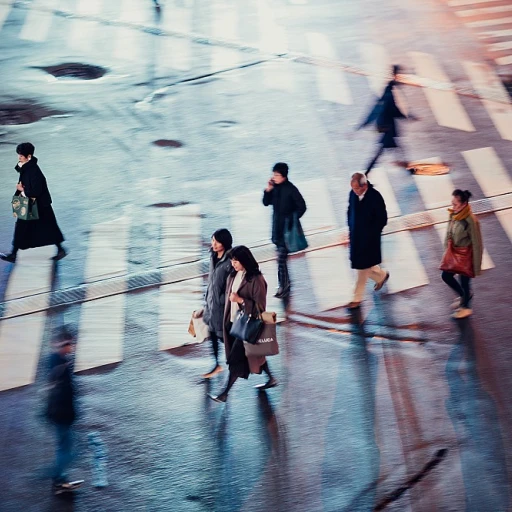
Understanding the Importance of TPM in Continuous Learning
The Role of TPM in Continuous Learning
Total Productive Maintenance (TPM) is a cornerstone in the realm of continuous learning, especially within production environments. It emphasizes the importance of proactive and preventive maintenance to maximize equipment effectiveness and minimize downtime. By integrating TPM into continuous learning strategies, organizations can significantly enhance their operational efficiency and quality.
Why TPM Matters
TPM is not just about maintaining equipment; it's about fostering a culture of continuous improvement and learning. This approach encourages operators to take ownership of their equipment, leading to better performance and fewer stops. The focus on autonomous maintenance empowers workers to identify potential issues before they become significant problems, thus reducing big losses and improving overall equipment effectiveness (OEE).
Continuous Improvement through TPM
Implementing a TPM program involves regular training and the use of a detailed checklist to ensure all maintenance tasks are performed consistently. This structured approach helps in identifying areas for improvement and facilitates a systematic review of processes. By using a checklist template, operators can follow a step-by-step guide to maintain equipment reliability and safety.
Linking TPM to Workforce Development
Incorporating TPM into daily routines not only improves production but also contributes to workforce development. As operators engage with TPM checklists, they gain valuable skills and insights, which are crucial for their professional growth. For more insights on overcoming challenges in workforce development, you can explore this resource.
Key Components of an Effective TPM Operator Checklist
Critical Elements of a Top-Tier TPM Operator Tool
In the realm of continuous improvement and total productive maintenance (TPM), crafting a well-rounded checklist is pivotal. This tool serves as a cornerstone in the quest to enhance equipment effectiveness and streamline operations. By laying out clear guidelines, the checklist ensures that maintenance tasks are consistently performed, reducing significant stops and minor disruptions in production cycles.
A quality checklist integrates several core components, each pivotal in enabling effective TPM. These include detailed maintenance tpm guidelines that focus on the equipment's specific needs, safety measures to prevent mishaps, and measures geared towards identifying and mitigating big losses. Such proactive steps not only optimize productivity but also enhance quality and reliability, ensuring that total production processes run smoothly.
Furthermore, an operator checklist must consider the training of personnel. This involves equipping team members with the necessary skills to execute autonomous maintenance and manage small stops efficiently. Continuous improvement is championed through regular training sessions that empower operators to perform thorough TPM audits and utilize the audit checklist effectively.
A robust template should also account for factors that could hinder TPM efforts, such as slow cycles and planned maintenance interruptions. Establishing a comprehensive check list helps in preempting production loss and promotes a culture of transparent management, whereby each step in the checklist template is documented and actions are consistently evaluated for performance improvement. By focusing on these components, an effective checklist not only bolsters equipment reliability but also integrates seamlessly into daily routines, fostering a proactive approach to maintenance management.
For further insights on crafting effective TPM strategies, explore these essential interview questions that can aid in selecting the right personnel for implementation and management.
Creating a TPM Operator Checklist PDF for Easy Access
Designing a User-Friendly checklist PDF
To effectively utilize Total Productive Maintenance (TPM) strategies, crafting a practical and accessible operator checklist PDF is crucial. This ensures that important maintenance activities are performed consistently, fostering continuous improvement in equipment reliability and operator performance.
Here's how you can create a valuable TPM checklist template in a PDF format to enhance your training and management initiatives:
- Simplicity and Clarity: The checklist should be clear and concise. Avoid unnecessary jargon and ensure the layout is simple to follow. This will facilitate ease of use for operators, making it easier to complete maintenance tasks efficiently.
- Comprehensive Coverage: Include all critical steps such as planned maintenance activities, autonomous maintenance tasks, and safety checks. This comprehensive coverage can help prevent small stops, slow cycles, and other breakdowns affecting overall equipment effectiveness (OEE).
- Visual Aids: Incorporate visual aids where possible. Diagrams, tables, and icons can quickly capture the operator's attention and provide clear guidance. For instance, a table that lists maintenance tasks against time frames can be particularly helpful.
- Flexibility and Customization: The template should allow flexibility for adaptation to different types of equipment. Customizable PDF checklists can be tailored to the specific requirements of different production environments or TPM audit processes.
- Ease of Distribution: By having the checklists in a PDF format, you ensure they are easily accessible and distributable across various platforms. Operators can download it onto their devices, allowing quick reference during maintenance tasks.
Creating this TPM checklist PDF not only aids in systematizing maintenance routines but also plays a vital role in tracking performance and quality improvement. By delving into the structured approach, organizations can effectively identify equipment losses and mitigate big losses caused by unplanned stops.
Integrating TPM Checklists into Daily Routines
Integrating TPM Checklists Seamlessly into Everyday Operations
Incorporating a Total Productive Maintenance (TPM) checklist into daily routines is essential for enhancing equipment reliability and ensuring optimal production quality. By making the checklist an integral part of the team’s daily management agenda, operators and maintenance staff can improve overall equipment effectiveness (OEE) while minimizing big losses from equipment failure. Creating a daily practice around the checklist involves several thoughtful steps:- Consistent Usage: The TPM checklist should be treated as an indispensable tool, used regularly to monitor maintenance tasks and identify slow cycles or small stops before they evolve into significant disruption. Operators must be trained to understand and value its importance, reinforcing the critical role of the checklist in continuous improvement and equipment performance.
- Customization: Each checklist should be tailored to the specific needs of the individual equipment. Modifying the template to align with the unique maintenance tpm requirements allows operators to efficiently identify and address issues that could lead to loss or reduced performance.
- Simplified Access: Make the checklist easily accessible, be it in a PDF format or as part of a maintenance checklist management system. The user-friendly format encourages operators to engage with the checklist frequently, ensuring comprehensive audits and proactive stops management.
- Autonomous Maintenance: Empower operators by integrating the checklist into autonomous maintenance routines. This approach fosters accountability and self-reliance, boosting confidence in handling day-to-day maintenance without constant supervision.
- Regular Updates and Training: As part of the TPM program, the checklist and associated training should evolve to reflect technological advancements and updated audit practices. Regular tpm audits ensure ongoing effectiveness and improvement in operational routines.
Challenges in Implementing TPM Checklists
Overcoming Barriers in Implementing TPM Checklists
Implementing a Total Productive Maintenance (TPM) checklist can be a transformative step towards enhancing equipment reliability and operator performance. However, several challenges can arise during this process, potentially hindering the effectiveness of the TPM program.
Resistance to Change
One of the primary obstacles is resistance to change. Operators and maintenance staff may be accustomed to traditional methods and skeptical about adopting new practices. To address this, it's crucial to emphasize the benefits of TPM, such as improved equipment effectiveness and reduced big losses. Training sessions and open discussions can help in easing this transition.
Complexity of Checklists
Another challenge is the complexity of the TPM checklist itself. A checklist that is too detailed or cumbersome can lead to confusion and errors. It's essential to create a checklist template that is clear, concise, and easy to follow. This ensures that operators can efficiently perform maintenance tasks without unnecessary stops or slow cycles.
Integration into Daily Routines
Integrating TPM checklists into daily routines can also be difficult. Operators may struggle to incorporate new steps into their established workflows. To facilitate this, management should encourage the use of checklists as part of the daily routine, highlighting their role in continuous improvement and safety. Regular audits and feedback can help identify areas for improvement and ensure compliance.
Resource Allocation
Effective implementation of TPM checklists requires adequate resources, including time, personnel, and training. Organizations must be willing to invest in these areas to achieve the desired outcomes. Planned maintenance and autonomous maintenance should be supported by a well-structured training program that equips operators with the necessary skills.
Measuring Success
Finally, measuring the impact of TPM checklists on operator performance can be challenging. It's important to establish clear metrics, such as Overall Equipment Effectiveness (OEE), to evaluate the success of the TPM program. Regular reviews and adjustments to the checklist can help in identifying performance gaps and driving continuous improvement.